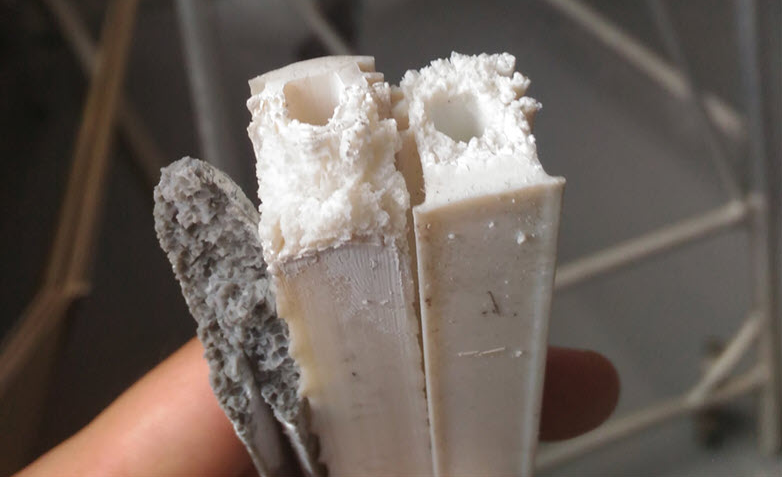
Improving Extreme Temperature Degradation of Silicone Rubber Using Flame Retardant Additives
Silicone rubber is well known for its durability at high temperatures. While other polymers such as nitrile, polyacrylate, and polyurethane have maximum service temperatures of around 70-150oC, silicone can withstand operating environments around 200-250oC. However, exposure to extreme temperatures will cause the silicone to combust. A common way to improve the resistance to extreme temperatures and fire is to include flame retardant additives in the manufacturing process. Not only does this increase the ignition temperature of silicone, but it also increases the durability of silicone at high temperatures and changes the way it combusts. Jehbco’s flame retardant silicones have been tested under AS1530.3, EN45545 and other standards to guarantee your peace of mind for high-temperature applications.
Silicone rubber has exhibits unique behavior at elevated temperatures. While most plastics will begin to melt at high temperatures, silicone does not have a melting point and remains solid until combustion occurs. At high temperatures (200-450oC), silicone rubber will slowly lose its mechanical properties over time, becoming brittle. The exact autoignition temperature of silicone depends on many factors such as the hardness of silicone, curing catalyst and any additives used. The standard autoignition temperature is around 450oC.
Silicone also exhibits unique behaviour during the combustion process. As the autoignition temperature is reached, the sample will smoke briefly before it begins to crack and combust. The silicone will expand in volume as volatiles are released, before the brittle combusted silicone breaks away from the sample, and will disintegrate into a fine powder upon any application of pressure. Silicone rubber primarily consists of a silicon-oxygen-silicon backbone with various carbon-containing methyl and vinyl groups. Upon combustion, silicon dioxide and carbon oxides are produced. The carbon monoxide and dioxide gasses are released into the atmosphere, while the silicon dioxide, as shown in Figure 1, creates a layer of white powder on the surface of the sample. This layer of silicon dioxide cannot be combusted further and acts as an insulating layer to help slow down and prevent further combustion of silicone.

Figure 1: Insulating silicon dioxide powder forming on a combusted silicone rubber sample
At Jehbco, we have been researching and developing new silicone rubber for over 40 years. Our flame retardant silicones have had extraordinary success in improving the flame retardant properties of silicone rubber. As shown in Figure 2, two different levels of flame retardant silicone were combusted along with a standard silicone rubber sample. The flame retardant silicone both ignited at higher temperatures than silicone rubber, and the extent of damage in the samples after combustion is much lower than the standard silicone rubber.
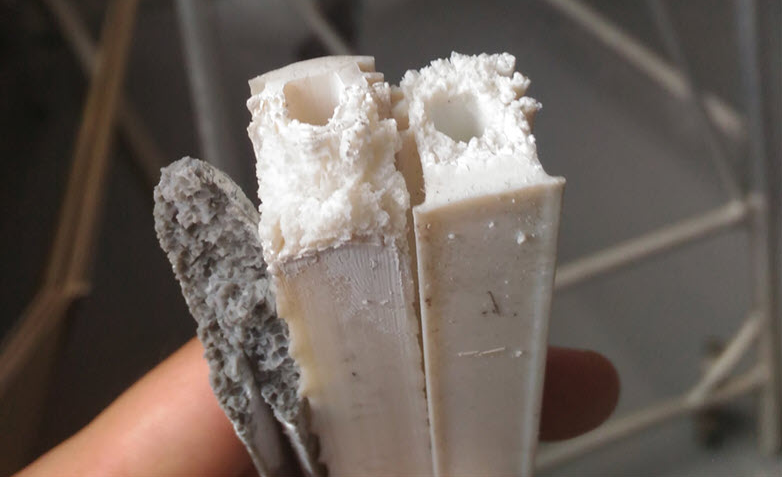
Figure 2: Combustion of standard silicone rubber (left) compared to various flame retardant silicone (right)
Ultimately, if you are looking for a reliable construction material for high-temperature applications, Jehbco’s flame retardant silicones are among the most durable and reliable materials available on the market. For further information or advice about which flame retardant silicone best suits your application, please review the Jehbco website www.jehbco.com.au, and contact us with any questions.