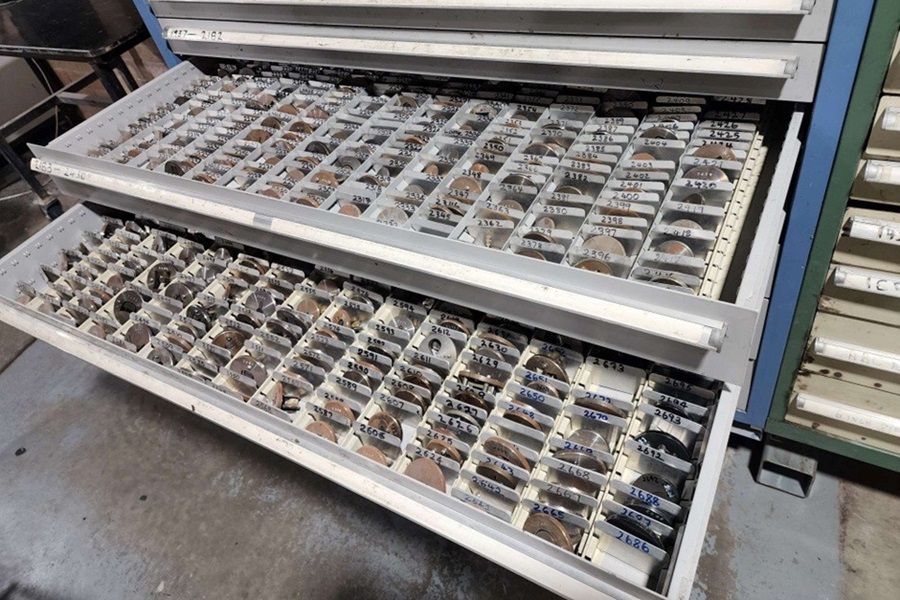
Creating Bespoke Silicone Solutions with Custom Dies: The Science Behind Extrusion Die Design
Custom extrusion dies play a critical role in the silicone extrusion manufacturing process, transforming raw silicone material into precise shapes required for countless industrial applications. Jehbco Silicones, a leader in high-quality silicone extrusion, supplies critical components to a range of industries, including food, medical, defence, aerospace, construction, and more. With a vast library of over 2700 unique extrusion dies, Jehbco enables unparalleled flexibility and precision in delivering custom extrusion profiles. From initial design to the final product, Jehbco’s extrusion process reflects a commitment to precision engineering and an understanding of the unique behaviours of silicone during extrusion.
The Challenges of Silicone Extrusion
Silicone rubber is a popular material choice because of its flexibility, elasticity, and malleability. However, these same qualities make silicone extrusions significantly more challenging to execute with dimensional accuracy than other commonly extruded materials such as metals. While metals are generally stable during extrusion and retain consistent dimensions after exiting the die, silicone’s elastic and deformable nature means that controlling its exact dimensions is far more complex.
1. Elasticity and Deformation
Unlike metals, silicone rubber is highly elastic and prone to expanding, compressing, and deforming both during and after extrusion. As a viscoelastic material, silicone rubber changes shape as it exits the die, making it difficult to achieve precise dimensions in the final extrusion. This elasticity causes immediate post-extrusion swelling, known as die swell or the Barus effect, where the silicone recovers its shape and expands slightly once the shear stress of extrusion is removed. Jehbco’s engineers work meticulously to account for these factors by adjusting die geometry and closely monitoring extrusion parameters.
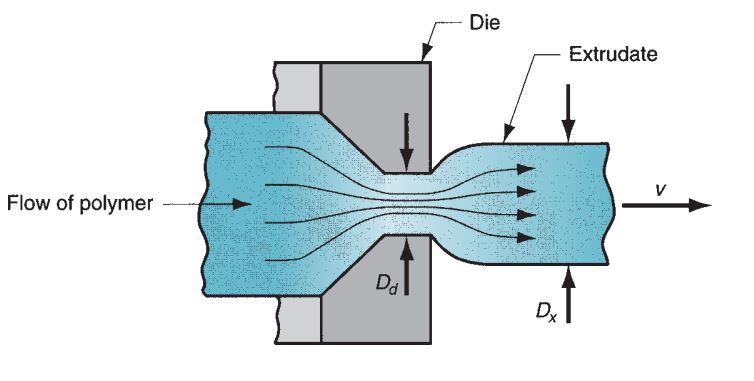
Figure 1. Die swell, a manifestation of viscoelasticity in polymer extrusions, as depicted here on exiting an extrusion die. The extruded material “remembers” its former shape and attempts to return to it after leaving the die orifice.
2. Thermal Expansion and Contraction
During the curing process, the silicone is subject to high temperatures. As silicone rubber has a high thermal expansion coefficient, it changes size more significantly with temperature variations compared to other commonly extruded materials (see Table 1). These thermal expansions and contractions create additional challenges in achieving consistent dimensions. Jehbco’s engineers carefully account for these properties when designing extrusion dies, calculating dimensions that accommodate potential thermal shifts during both extrusion and curing processes. By considering these factors, Jehbco can create extrusion dies that maintain dimensional consistency, even under changing temperature conditions.
Table 1. Coefficients of Thermal Expansion (CTE) of Commonly Extruded Materials
Material |
Expansion Coefficient |
Alumimium |
21.0 – 24.0 |
Brass |
18.0 – 19.0 |
Copper |
16.0 – 16.7 |
Nickel |
13.0 |
Polyethylene (PE) |
100-200 |
Polypropylene (PP) |
100-180 |
Polystyrene (PS) |
30 to 210 |
Silicone Rubber |
200 to 400 |
Titanium |
8.5-9.0 |
3. Post-Extrusion Curing
Another challenge lies in the curing process. Silicone extrusions undergo vulcanisation curing to solidify and stabilize their final shape. During the curing process, the cross-linking of rubber molecules can cause the silicone to unpredictably shrink or expand, complicating the task of dimensional accuracy. Jehbco’s team manages this through iterative die adjustments, fine-tuning the process to accommodate these changes and produce profiles that meet our customer’s precise specifications.
Understanding Die Swell in Silicone Extrusions
Die swell is a phenomenon in extrusion where the material expands upon exiting the die, a behaviour influenced by silicone’s viscoelastic properties. As a viscoelastic material, silicone exhibits both elastic and viscous characteristics, which result in an elastic recovery effect after it leaves the die. The extent of die swell depends on several factors, each of which Jehbco’s engineers carefully consider when designing and refining custom extrusion dies.
- Die Design
The geometry of the die plays a crucial role in determining the amount of swell. Dies with a longer land, the straight portion at the die exit, allow the silicone to relax more before leaving the die, reducing the degree of swell. In contrast, shorter lands may result in more significant expansion. Jehbco’s engineers consider each die’s length, taper, and overall shape to achieve optimal results for each extrusion. - Silicone Rubber Hardness and Viscoelasticity
Silicone’s elasticity contributes to its tendency to swell, especially under high deformation. During extrusion, the high shear rates within the die force the silicone into a compressed state. As the silicone exits, its elastic properties prompt it to expand, creating the swell. Silicone rubber with a higher Shore A hardness rating will extrude with much less die swell than that of low hardness, producing extrusion profiles much closer to original die profile. - Extrusion Speed
Higher extrusion speeds tend to increase the degree of swell due to greater molecular alignment and shear rates. Jehbco carefully calibrates extrusion speed according to the specific die and material properties, balancing efficiency with dimensional precision to ensure the final product meets specified tolerances. - Temperature
The temperature of the silicone and the die affects both viscosity and elasticity. Higher temperatures reduce viscosity, allowing the silicone to flow more easily, but can also enhance its elastic recovery and thus influence the degree of swell. Jehbco’s engineers monitor and control temperature conditions to optimize extrusion consistency, balancing temperature settings to achieve desired properties in the final product. - Processing Conditions
Beyond the die itself, other factors like extrusion pressure and cooling rates post-extrusion can impact the final product’s dimensions. Managing these variables carefully, Jehbco ensures that products remain within required tolerances by adjusting extrusion pressure and cooling rates to control the extent of swell and prevent dimensional deviations.
The Iterative Process of Fabricating Custom Dies
Creating a custom extrusion die is a complex process involving iterative adjustments, each bringing the extrusion profile closer to the desired specifications. Initial tests with a new die may reveal major discrepancies in dimensions, requiring significant modifications to compensate for the extreme die swell in the extrudate. Jehbco’s iterative process, informed by decades of experience, ensures that each custom die meets the precise requirements of the application.
With each iteration, Jehbco’s skilled engineers adjust factors like the die’s profile, land length, internal bridge configuration, and other design aspects to achieve the final profile. This iterative refinement process ensures the resulting extrusion meets exacting standards, delivering profiles that perform as expected in real-world applications. Furthermore, recent revolutionary advancements of the custom die fabrication process at Jehbco have allowed us to push the limit of what is possible and achieve even tighter tolerances than ever before.
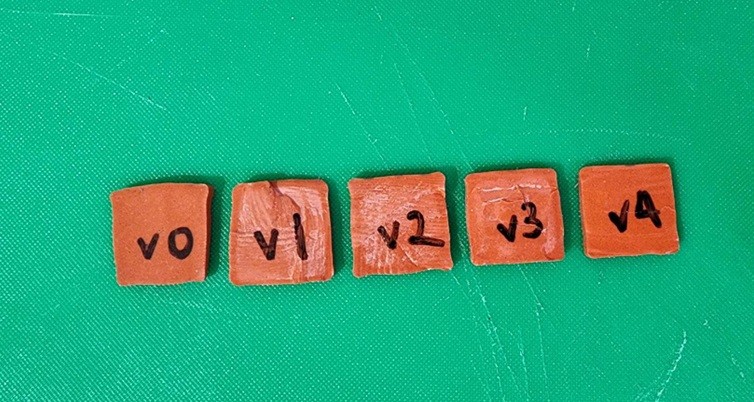
Figure 2. Iterations of a custom square profile extrusion (25.4mm x 25.4mm). Excessive die swell present in the initial extrusion (pictured left) was reduced with each iteration.
Precision Cutting with the Excetek V400G Wire EDM Machine
Jehbco employs the advanced Excetek V400G wire EDM (Electrical Discharge Machining) machine to cut extrusion dies with exceptional precision, achieving tolerances as tight as ±5µm. This capability is essential in silicone extrusion, where even the smallest variations in die dimensions can result in deviations from specified tolerances in the final product. By leveraging wire EDM technology, Jehbco ensures that each die meets stringent design specifications, guaranteeing repeatability and accuracy across production runs.
The V400G wire EDM machine allows Jehbco to quickly adapt to custom profiles, providing high-quality, consistent dies for even the most intricate shapes. Its precision helps mitigate potential issues related to die swell, a phenomenon common in silicone extrusion, by creating dies that account for silicone’s unique material properties and extrusion behaviour.
Expanding Possibilities with Jehbco’s Custom Extrusion Solutions
Jehbco’s extensive library of extrusion dies—comprising over 2700 unique designs—serves as a testament to the company’s expertise and flexibility in custom silicone extrusions. These dies enable Jehbco to accommodate an array of application requirements across industries, from healthcare to automotive and beyond. Whether designing seals for high-temperature environments or gaskets with complex internal channels, Jehbco leverages its knowledge of die swell, extrusion dynamics, and precision machining to deliver quality silicone profiles.
Using the Excetek V400G wire EDM machine, Jehbco provides clients with unparalleled accuracy and flexibility in custom extrusion dies, opening doors to applications where precision and consistency are paramount. By balancing material properties, temperature, extrusion speed, and other factors, Jehbco controls die swell and ensures high-quality, reliable products with each extrusion.
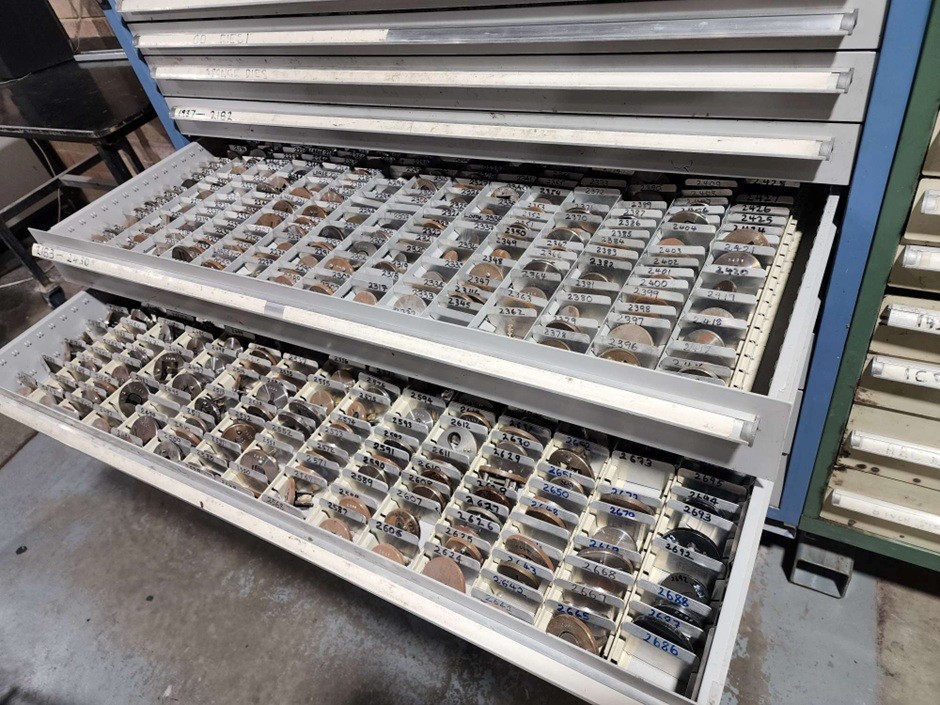
Figure 3. Jehbco’s vast library of over 2700 custom extrusion dies.
Partnering with Jehbco for Precision Custom Extrusions
With the right extrusion die, silicone’s unique properties can be harnessed to deliver highly durable, flexible, and custom-tailored components. Jehbco’s dedication to precision engineering and its understanding of silicone behaviour make it a trusted partner for businesses in the food, medical, defence, aerospace, construction, and other industries seeking custom extrusions. Through rigorous quality control, iterative refinement, and the use of cutting-edge technology, Jehbco Silicones stands at the forefront of silicone extrusion, committed to meeting each customer’s specific needs with precision and expertise.
Whether for a small-scale custom order or large production runs, Jehbco’s custom extrusion dies enable the creation of silicone profiles that fulfill stringent requirements and perform reliably in demanding applications. For more information or enquiries, please email sales@jehbco.com.au for a quick response from our sales team.
References
- M.P. Groover, Fundamentals of Modern Manufacturing: Materials, Processes, and Systems, 4th Edition, Wiley, 2010, pg. 271
- https://www.engineeringtoolbox.com/linear-expansion-coefficients-d_95.html
- https://www.professionalplastics.com/professionalplastics/ThermalPropertiesofPlasticMaterials.pdf
- https://www.dryseals.com/app/uploads/2016/09/Basic-Info-Wacker.pdf
- https://www.engineeringtoolbox.com/linear-expansion-coefficients-d_95.html
- https://link.springer.com/chapter/10.1007/978-94-011-4421-6_22