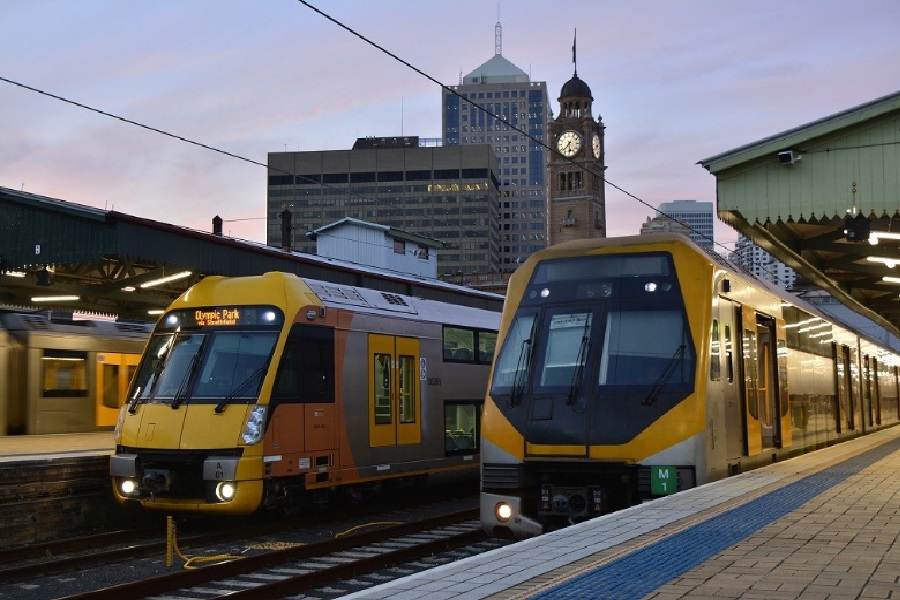
From Material Properties to Applications: The Role of Silicone Rubber Extrusions in Modern Industries
Silicone rubber is one of the most versatile and widely used materials in modern manufacturing and engineering. Its exceptional physical, chemical, and thermal properties make it indispensable across industries such as construction, defence, medicine, electronics, food processing, and more. Silicone rubber has numerous advantages over natural rubber, including superior temperature resistance, chemical inertness, and durability, making it the material of choice for demanding applications.
This article explores the unique material properties of silicone rubber, its advantages over natural rubber, and the diverse applications of silicone extrusions across industries.
Material Properties of Silicone Rubber
Silicone rubber is a synthetic elastomer made from a polymer backbone of silicon, oxygen, and organic groups. Its structure gives it a unique combination of properties that set it apart from other materials. Below are the key properties of silicone rubber:
1. Temperature Resistance
Silicone rubber can withstand a wide temperature range, from as low as -60°C to as high as 230°C (and even higher for specialized grades). Unlike natural rubber, which becomes brittle at low temperatures and degrades at high temperatures, silicone rubber retains its flexibility and performance across extreme conditions. This makes it ideal for applications in environments with temperature fluctuations, such as automotive engine bays, industrial ovens, and aerospace components. [1]
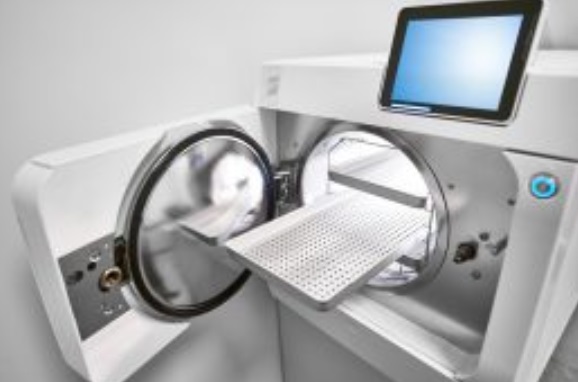
Figure 1. An autoclave with a silicone extrusion door seal, used to sterilise surgical instruments. Silicone rubber’s excellent material properties make it ideal for applications such as these.
2. Chemical Inertness
Silicone rubber is highly resistant to a wide range of chemicals, including oils, solvents, and many acids and bases. This chemical inertness ensures that it does not degrade or react in harsh environments, making it suitable for applications in marine environments, medical and food-grade systems, and chemical processing. [2]
3. UV, Ozone, and Weather Resistance
Unlike natural rubber, silicone rubber is inherently resistant to UV radiation, ozone, and weathering. These properties make it ideal for outdoor applications and exposure to harsh environments. For example, Jehbco has developed silicone door hatch seals for ships in the marine industry. These seals protect door hatches from the damaging effects of saltwater, UV rays, and weather conditions, ensuring long-lasting performance even in the harsh marine environment. Such applications highlight silicone’s superiority in resisting environmental degradation. [3]
4. Flexibility and Elasticity
Silicone rubber maintains its flexibility and elasticity across its temperature range. It can stretch, compress, and bend without losing its structural integrity, making it ideal for seals, gaskets, and tubing that need to accommodate movement or pressure changes. Furthermore, silicone’s flexibility makes it ideal for forming tight seals as it readily deforms to fill the empty spaces of its mating parts. [4]
5. Non-Toxic and Biocompatible
Silicone rubber is non-toxic, hypoallergenic, and biocompatible, making it a trusted material in medical and food-grade applications. For example, it is used in medical implants, catheters, and food processing seals. Medical-grade silicone is used in products that come into direct contact with the human body, such as catheters, implants, and prosthetics.
For example, Jehbco has developed high-quality tubing for filtered water systems. Our silicone tubing ensures hygienic fluid transfer in water filtration systems, providing chemical resistance and preventing contamination. Additionally, Jehbco has contributed to the healthcare industry by manufacturing silicone tubing used in vaccine development processes, where sterility and biocompatibility are paramount. These applications demonstrate the versatility and safety of silicone in industries that demand the highest levels of performance and hygiene. [5]
6. Electrical Insulation
Silicone rubber is an excellent electrical insulator, providing reliable protection for wires and electronic components in high-voltage, high-temperature, and wet environments. Jehbco has produced silicone cable sleeves for high-voltage electrical cabling that are flexible yet durable, protecting the inner cables from harsh environments.
7. Customizability
Silicone rubber can be formulated into different grades, colours, and hardness levels, and can be extruded into virtually any shape and size, allowing for custom solutions tailored to specific applications.
Advantages of Silicone Rubber Over Natural Rubber
While natural rubber has been a staple in manufacturing for decades, it has limitations that silicone rubber overcomes. Silicone rubber has vastly superior properties, making it the preferred material for demanding applications. The key advantages of silicone rubber over natural rubber include:
- Temperature Range: Silicone rubber can withstand extreme temperatures, typically ranging from -60°C to 230°C, and up to 300°C for specialized grades. This makes them ideal for applications exposed to high heat or freezing cold, such as industrial ovens, engine components, and outdoor seals. This is vastly superior to natural rubber which is limited to just -20°C to 70°C and cannot withstand extreme temperatures as silicone rubber can. Natural rubber becomes brittle at low temperatures and degrades in high-heat environments while silicone remains perfectly stable in such environments.
- Weather Resistance: Natural rubber is prone to degradation when exposed to UV rays, ozone, and weathering, whereas silicone rubber is highly resistant to these factors.
- Chemical Resistance: Silicone rubber remains stable when exposed to oils, solvents, and corrosive chemicals, making it more durable in harsh environments. However, natural rubber swells and deteriorates in similar conditions. This makes silicone rubber indispensable in chemical plants and automotive fuel systems.
- Shelf-life: Silicone rubber has an extremely long lifespan of 20 years or even longer with proper storage, thanks to its resistance to environmental and chemical degradation. Natural rubber, on the other hand, is prone to oxidation and degradation over time. [1]
- Biocompatibility: Natural rubber contains latex proteins, which can cause allergic reactions in some individuals. Silicone rubber, being non-toxic and hypoallergenic, is widely used in medical and food-grade applications. [5]
Table 1. Advantages of Silicone Rubber Over Natural Rubber
Property |
Silicone Rubber |
Natural Rubber |
Temperature Range |
-60°C to 230°C (up to 300°C for some grades) |
-20°C to 70°C |
Weather Resistance |
Highly resistant to UV, ozone, and weathering |
Degrades under UV and ozone exposure |
Chemical Resistance |
Resistant to oils, solvents, acids, and bases |
Vulnerable to oils and solvents |
Longevity and Durability |
Long-lasting, durable in harsh conditions |
Degrades faster under environmental stress |
Biocompatibility |
Hypoallergenic, non-toxic, biocompatible |
May cause allergic reactions (latex) |
Customizability |
Wide range of formulations and applications |
Limited adaptability to extreme conditions |
Microbial Resistance |
Resistant to bacteria and fungi |
Prone to microbial growth |
Applications of Silicone Extrusions in Various Industries
Thanks to its excellent material properties, silicone extrusions have found applications in countless industries, offering custom solutions for seals, gaskets, tubing, and more. Indeed, Jehbco Silicones have been producing silicone extrusions for over 50 years to both Australian and international customers, and our products can be found everywhere from flame retardant door seals on trains, ships and planes, to filtered water systems in your home to architectural gap seals such as Quickjoint, just to name a few.
Below are some more applications of our silicone extrusions:
- Healthcare and Medical
The biocompatibility and sterility of silicone rubber make it essential in the medical field.
- Medical Tubing: Silicone extrusions are used for fluid transfer in catheters, peristaltic pumps, and respiratory devices due to their flexibility and non-toxicity.
- Seals and Gaskets: Silicone seals ensure a sterile and reliable environment in medical devices and laboratory equipment.
- Prosthetics and Implants: Medical-grade silicone extrusions are used for implants and prosthetics because of their hypoallergenic nature and durability.
- Automotive, Aerospace and Transportation
Silicone extrusions play a critical role in enhancing vehicle performance and durability.
- Weatherstripping and Door Seals: Silicone seals prevent water and air leaks while reducing road noise.
- Engine Components: High-temperature silicone tubing and gaskets are used in engine compartments to handle heat and chemical exposure.
- Vibration Dampening: Silicone extrusions absorb vibrations, improving vehicle comfort and reducing noise.
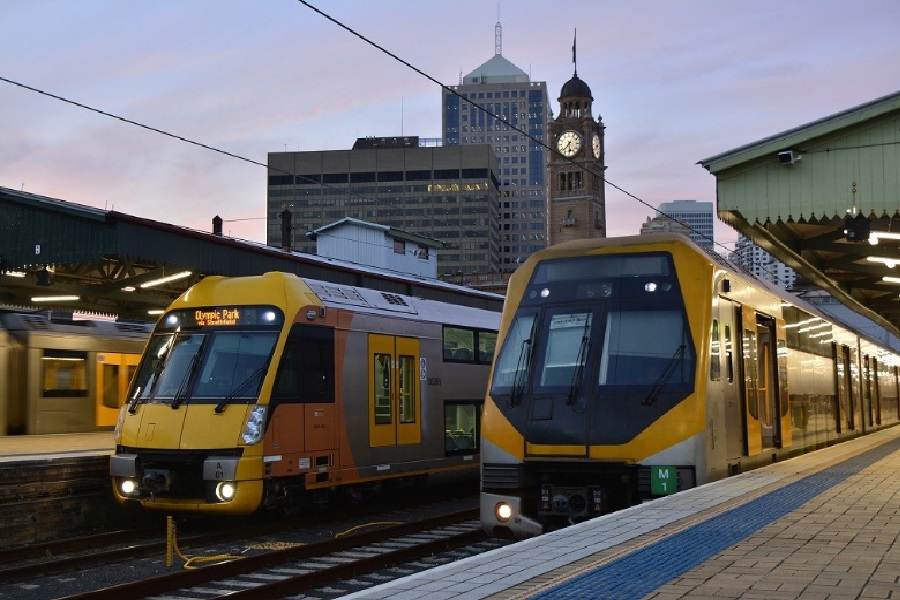
Figure 2. Sydney Metro Trains, one of the many applications of Jehbco’s silicone extrusions.
- Construction and Architecture
Silicone extrusions are widely used in construction due to their durability and weather resistance.
- Window and Curtain Wall Seals: Silicone gaskets provide airtight and watertight seals, ensuring energy efficiency and protection against the elements.
- Expansion Joints: Flexible silicone extrusions accommodate thermal expansion and contraction in buildings, bridges, and roads.
- Roofing and Façade Systems: Silicone seals and gaskets enhance the longevity of building exteriors by resisting UV radiation and weathering.
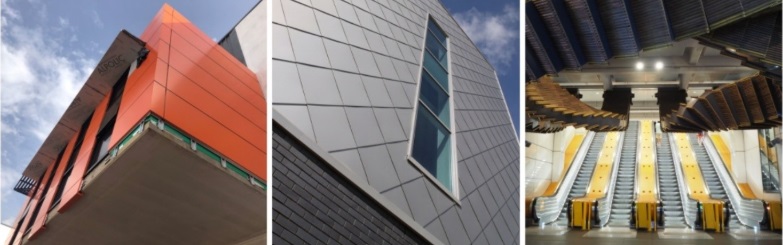
Figure 3. Applications of Quickjoint by Jehbsil, a custom engineered solid silicone solution for architectural gap seals.
- Electronics and Electrical Engineering
Silicone extrusions protect sensitive components in challenging environments.
- Cable Insulation: Silicone tubing provides electrical insulation and protects wires from moisture, heat, and chemical exposure.
- Seals for Electronic Enclosures: Silicone gaskets ensure a watertight and dustproof seal for devices used in harsh conditions.
- LED Lighting: Silicone extrusions shield LEDs from environmental factors, improving performance and durability.
- Food and Beverage
The non-toxic and food-grade properties of silicone rubber make it ideal for food processing and packaging.
- Food-Grade Tubing: Silicone tubing is used for transferring liquids and food products in hygienic conditions. It is easy to clean, resistant to contamination, and compliant with food safety standards.
- Oven and Freezer Seals: Silicone extrusions are used in ovens, refrigerators, and freezers due to their ability to withstand extreme temperatures.
- Industrial Applications
Silicone extrusions enhance performance and efficiency in industrial settings.
- Heat-Resistant Seals: Silicone gaskets are used in industrial ovens, kilns, and autoclaves where they maintain performance under extreme heat.
- Chemical Transfer Systems: Silicone tubing is ideal for transporting chemicals in manufacturing processes due to its resistance to corrosion and degradation.
- Conveyor Belts and Rollers: Silicone extrusions are used in machinery components that require high friction and temperature resistance.
- Renewable Energy
Silicone extrusions contribute to the durability and efficiency of renewable energy systems.
- Solar Panel Seals: Silicone gaskets and extrusions provide weatherproof seals for solar panels, protecting them from moisture and dirt.
- Wind Turbine Components: Silicone extrusions are used for sealing and vibration dampening in wind turbines.
Conclusion
Silicone rubber is a game-changing material with properties that outshine natural rubber in many aspects, including temperature resistance, chemical inertness, and durability. Its ability to be extruded into custom profiles makes it a versatile solution for a wide range of industries, from healthcare to construction and electronics.
Jehbco Silicones has exemplified the versatility of silicone with its innovative solutions, such as tubing for filtered water systems and components for vaccine production in the medical field. These applications highlight the importance of silicone in solving real-world challenges and improving efficiency and safety across industries.
For companies seeking high-quality silicone extrusions, working with Jehbco Silicones can unlock new possibilities and ensure precision-engineered solutions tailored to specific needs. Silicone rubber is truly the material of the future, offering versatility, durability, and performance that stands the test of time.
References
- SpecialChem. Silicone Rubber Properties and Applications.https://omnexus.specialchem.com/selection-guide/silicone-rubber-elastomer
- AZoM Materials Science. Properties of Silicone Rubber. https://www.azom.com/properties.aspx?ArticleID=920
- Dow Corning. Silicone Rubber Handbook. Retrieved from https://www.dow.com/en-us.html
- Vanguard Products. Silicone Properties and Benefits. Retrieved from https://www.vanguardproducts.com/silicone-properties
- Medical Design BriefsSilicone in Medical Applications. Retrieved from https://www.medicaldesignbriefs.com/