Jehbco Silicones provides a wide range of tubing products:
- Internal diameters can start from 0.5 mm
- Outside diameters can go up to 60 mm
- Different hardnesses (durometers) are available
- Different colours are available
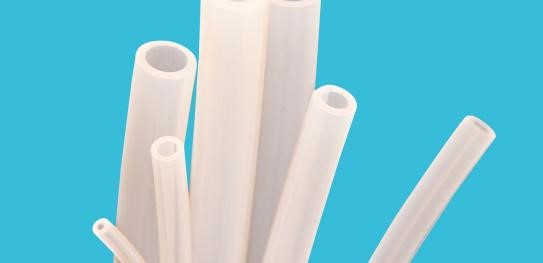
Figure 1: Different sizes of transparent silicone tubing
Jehbco’s tubing is primarily used for fluid transfer:
- Water transfer for boiling and chilled appliances
- Fluid transfer in medical application
- Fluid transfer in batteries or engines specific to the automotive or energy industries
- Fluid transfer in precision scientific equipment for science industry (ie. laboratories)
Our tubing for water and medical applications are made of platinum rubber. These products are thoroughly post cured to further decrease levels of extractables. The process is integral so our tubing is compliant with the AS/NZS 4020 standard. Jehbco has currently tested and complies with the AS/NZS 4020 standard for platinum 70 rubber for the following colours: transparent, red-transparent, blue-transparent and black transparent.
AS/NZS 4020 is a standard that is designed to test any products for use in contact with drinking water1. These products include tubing, pipes or any material used for applications in plumbing and water supply. The standard ensures that drinking water in contact with such products meet water quality values which are nationally recommended.
The standard provides methods of testing and compliance limits for the effect of a product/material2. For the different tests of the standard, products are immersed in water or exposed to substances. Each test has specific procedures and are specific to the type of product2. The different methods of testing are described below2:
Taste of water: “A trained panel tastes water extracts to determine whether products release any compounds that impart discernible taste”ii
Appearance of water: Colour or turbidity of the water extract is measured.
Ability of a product to support the growth of aquatic micro-organisms: Dissolved oxygen levels are monitored during 8 weeks to examine the ability of the product to support bacterial growth.
Cytotoxic activity of water extract: Water extract is placed in contact with mammalian cell lines. Any adverse effect on the cell health is considered as evidence of a cytotoxic effect.
Mutagenic activity of water extract: An AMES test is used. Specific bacteria are mixed with the water extract. Any change in the bacteria’s genetic nature is considered as evidence of mutagenic activity
Extraction of metals: Levels of arsenic, antimony, barium, cadmium, chromium, copper, lead, mercury, molybdenum, nickel, selenium and silver in the water extract are analysed and compared to the limits of the National Health and Medical Research Council (NHMRC) guidelines.
High-Temperature tests: Products in contact with hot water are tested at high temperaturesii.
Products are required to comply with all the tests relevant for that product type to be certified by AS/NZS 4020 standard. Jehbco’s tubing is regularly tested as the test reports for the AS/NZS 4020 test are valid for 5 years3.
To learn more about our silicone tubing, see our tubing page or contact us.
References
- Australian/New Zealand Standard, “AZ/NZS 4020 Standard` in SAI global limited website, viewed on 25th June 2019, https://www.saiglobal.com/PDFTemp/Previews/OSH/as/as4000/4000/4020-2005.pdf
- AWQC, “Overview of the Standard” in AWQC website. Viewed on 25th June 2019, https://www.awqc.com.au/our-services/product-testing/overview-of-the-standard
- Eurofins, “AS/NZS 4020 Test for Watermark™ Certification” in Eurofins website, viewed on 25th June 2019, https://www.eurofins.com.au/biopharma-services/testing-solutions/chemistry-toxicology/asnzs-4020-test-for-watermark-certification/